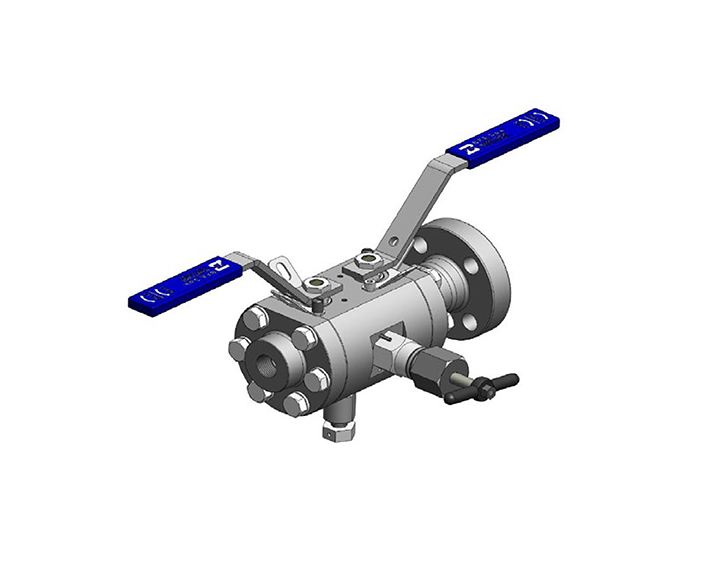
The increased activity in the offshore sector of the energy industry has led to additional factors that have to be taken into consideration when designing piping systems. Space in these modern locations is always at a premium and the design of piping systems and their associated components must therefore be more compact. There are structural constraints that are also very important, such as keeping the structure as light as possible, and there are obvious benefits from making components smaller and lighter. Construction site work is also very expensive and any reduction in installation manpower is also beneficial.
The above situation has led to the modification of the patterns of valve components to incorporate savings in space, weight, and labor costs where possible, while still retaining the original function of the valve. The greatest savings are to be seen in the reduction of leak to atmosphere because the potential leak points are minimized compared to the conventional design. Process isolation philosophy has become more complex as safety issues have to be addressed and the requirement for double block and bleed isolation has become more commonly used. Double Block and Bleed isolation requires two in-line isolation valves and a bleed valve, used to drain or vent trapped fluid between the two closure elements.
Double block and bleed valves replace existing traditional techniques employed by pipeline engineers to generate a double block and bleed configuration in the pipeline. Conventionally, in order to achieve a double block and bleed system, engineers would install two standard isolation valves and a separate facility for bleeding the cavity in between.
Space is usually at a premium in the refinery environment, and this approach requiring an additional valve unit to be installed as well as a “T”-junction to allow the cavity to be bled more than doubles the space required compared with a single valve system. This increase in size can often make the installation unfeasible, especially where multiple valves along the line are to be upgraded.
DOUBLE BLOCK AND BLEED MAIN FUNCTIONS
Instrument Double Block and bleed for chemical injection & sampling Double Block and Bleed valves for chemical injection & sampling require an additional straight tubing onto the bore of the valve inlet flange face. This quill enters into the process flow and chemicals can be introduced through the valve.
Incorporated in the valve design an additional check valve is required for this application in order to prevent reverse flow and process fluid contaminating the chemical source. For sampling the reverse is applied.
Instrument Double Block and bleed for pressure connections Double Block and Bleed valves for pressure connections are generally used to isolate instrumentation such as pressure indicators and lever gauges.
In-line Double Block and bleed for process isolation Double Block and Bleed valves for process isolation are located in the primary process stream.
Belfast Controls Equipment Trading LLC are the official distributor and stockiest in U.A.E market, and we stock Forged Gate Valves, Globe Valves, Check Valves, Ball Valves in Dubai
Applicable standard range
SIZE : From NPS 1/2 TO NPS 8 or From DN 15 TO DN 200
CLASS : From ASME 150 to ASME 2500
Applicable standards
Design : ASME B1634 and if applicable EEMUA 182 , ASME B16.34 , ISO 17292 , API 608 , ASME B16.34 , API 6D
Inspection & testing : API 598
Marking : MSS SP-25
Rating : ASME B16.34 With possible derating for high temperature based on seat material.
Fugitive emission : ISO 15848
Applicable end finishes
Face to face : Manufacturer standard.
End to end : Manufacturer standard.
Socket weld : ASME B16.11
Screwed ends (NPT) : ASME B1.20.1
Flanged ends : ASME B16.5
Butt welding ends : ASME B16.25
Product features
1). Floating or trunnion mounted ball valves in main bore, each valve is bi-directional and designed for full differential pressure at ambient and low temperature. For main bore valve general features see the ball valve sections (floating ball or trunnion ball).
2). Full die forged structure for all pressure containing parts.
3). Integral body comprising of two ball valves through main bore with a needle bleed valve from the cavity between the two ball valves. Housing design can be split body or end entry (end entry cannot be feasible for all range).
4). Standard primary gasket design is Lip-Seal type, secondary emergency seal always provided for fire-safe purpose.
5). High quality sealing products and reduced leakage points.
6). Improved safety in operations, space and weight.
7). Compact design.
8). Uninterrupted flow for negligible pressure drop.
9). Reduced stresses from loading and vibration.
10). Reduced installation and maintenance requirements.
11). Designed and engineered on a case-by-case basis.